Hybrid Actuators Position the Primary Mirror of the World's Largest Ground-Based Telescope for the Optimal Beam Path
The European - Extremely Large Telescope, in short ELT, of the European Southern Observatory (ESO) has a segmented main reflector with a diameter of 39 m, a light collecting area of almost 1,000 m², and is the largest telescope for scientific evaluation of electromagnetic radiation in the visible and near infrared wavelength range. It will be put into operation atop the 3,046-meter high Cerro Amazones in the Chilean Atacama desert during 2024. One of the most important tasks of the telescope is to help us to find out more about exoplanets, i.e., planets that exist beyond the solar system.
Project Requirements
The main reflector will be made up of 798 individual mirror elements each with a diameter of 1.40 meters. Altogether, the segments will collect several tens-of-millions more light than the human eye is capable of and transfer this light into scientific instruments via further optics. To compensate for deviation from the optimum beam path and therefore avoid imaging errors, the mirror elements must be aligned exactly to each other. Deviation from the optimum beam path can result for example, from distortion of the telescope tube because of gravitation, thermal effects or wind pressure.
Each mirror segment is positioned by three drives. The requirements push the technology to its limits: Relatively long travel ranges of up to 10 mm with a position and path accuracy of better than 2 nm are the challenges that need to be overcome when developing the actuators. Tracking an object during observation typically requires velocities of between several nanometers per second and +/- 0.45 µm/s. The average position deviation may not be more than 2 nm. If the telescope is to be aimed at a different object, velocities of up to +/- 100 µm/s are required. This involves moving considerable weights: A mirror segment weights 250 kg.
Due to the different alignments of the telescope, an individual drive has to move or hold loads between 463 N pulling force and 1050 N pushing force. Winds or an earthquake can cause these loads to be exceeded considerably, but the drives would then not be in an active operational state. Furthermore, the very high demands on the lifetime of the systems represents a considerable technical risk, which needs to be considered when realizing the project and the same applies to the maximum permissible exhaust heat for actuators and controllers. PI "customized" a hybrid drive for this very demanding task.
For more information on ESO and on the signing of the contract click >> here
Positioning Solutions for Mirror Elements
The principle of the hybrid drive combines a motor-spindle drive that is suitable for high loads and large travels with a piezo actuator. All inaccuracies of the motor-spindle drive can be measured with a high-resolution sensor and corrected using the piezo. This ensures an extremely high positioning accuracy that cannot be achieved with pure motor-spindle drives.
A dedicated controller controls both drives simultaneously and controls the high-resolution position measuring system. The servo algorithms consider the motor and the piezo system as a single drive unit and compare the actual motion with a calculated trajectory. This allows ESO to accurately compensate deformations in the structure of the primary mirror. The spindle is driven by a brushless high-torque motor via a high-ratio reduction gearhead. The gearhead ensures zero-play operation and guarantees a constant transmission ratio. The motor can therefore be very small even though large masses have to be moved. The high transmission also supports self-locking of the motor when at rest.
The piezo actuators are encapsulated in a closed metal bellows filled with nitrogen so that they are protected against moisture and achieve the lifetime of 30 years required for the positioning solu-tion, even under adverse ambient conditions. The high-resolution sensor is an incremental optical encoder, which is placed as close as possible to the axis of the drive. It operates at a resolution of 100 picometers and is insensitive to changing ambient conditions.
Electronics Design and Controller Structure
The drive electronics consist of two function blocks: The commutation electronics for the motor, the interpolation, and the limit switches are located directly in the drive housing. This allows short encoder lines to prevent signal interference. A single cable connects the drive to the second function block and the external electronics, which control the motor, piezo, and encoder. The main controller has three channels. This means that only one controller is required to control all three hybrid drives of a mirror segment. At the same time, it is possible to specify motion commands for each individual drive as well as the desired position of the mirror segment.
The controller then "translates" a command for its three axes. The control principle of the hybrid drive is easy to understand: The motor voltage is derived from the control voltage of the piezo. The greater this voltage, the faster the motor runs. When the piezo expands, the motor drives the spindle in the same direction. In this way, the coarse positioning of the spindle is supplemented by the fine positioning of the piezo. At the same time, the spindle always moves the piezo near to its zero position automatically. This gives it the best chance of correcting the position in both directions. In this way, relatively long travel ranges can be combined with an extremely high positioning accuracy.
The performance of the hybrid drive was confirmed during extensive testing at the ESO. The flexible controller concept is very much appreciated by everyone and this simplifies subsequent enhancement.
Downloads
Hybrid Nanopositioning Systems with Piezo Actuators
Long Travel Ranges, Heavy Loads, and Exact Positioning
Do you want to know more about our solutions? Our specialists are happy to help.
Contact us today!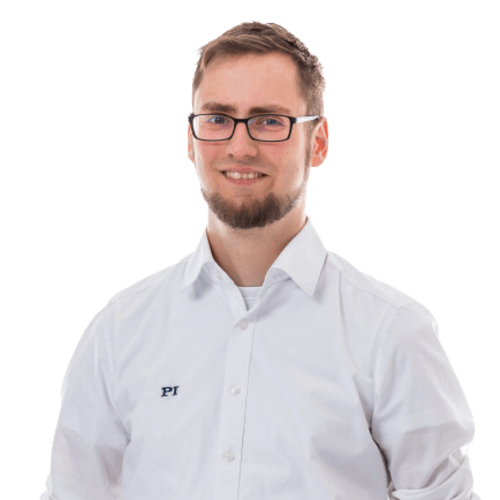