
Laser technologies continue to push the envelope of possibility in modern manufacturing and materials processing applications. The theory of stimulated electromagnetic radiation emission was first proposed by Einstein in 1917, but decades passed before physicists and engineers were able to generate spatially coherent beams of monochromatic light via this principle, and decades more were required for the technology to reach maturity. Almost 60 years on from the invention of the first fully-functioning laser, this technology is now a crucial component in the manufacturing and materials processing world. Today, lasers are used in a variety of cutting, drilling, marking, micromachining, and welding applications in virtually every consumer and industrial market. Lately, even the surface of pistons for automotive engines has been structured using femtosecond lasers – a step to reduce friction and improve fuel economy.
Precision Motion Control for Lasers Processing
Recent successes in laser processing come down to a tandem of progression in ultra-short pulse laser technologies, motion control and industrial automation. In order to direct the laser beam precisely to where its energy is needed, either the beam can be manipulated, or the sample that needs to be machined or processed may be manipulated instead. This is possible by steering the beam with a set of movable mirrors, often called a Galvo Scanner, or by moving the sample in the X and Y coordinate. High end solutions combine both methods to achieve greater precision and speed.
Especially when combining both methods, high performance motion controllers are required, as well as fast and accurate, closed-loop positioning stages that provide real-time position feedback to the controller to allow triggering of the laser at the exact moments. High end systems provide sub-micrometer (μm) levels of precision alongside fast acceleration for increased throughput.
Here, we offer a brief outline of the importance of precision motion control in laser cutting systems. Read this article for more information on laser surface processing.
How Does Laser Cutting Work?
Laser cutters use a focused beam of high energy light to trim or cut through a material via deposition of thermal energy. Continuous wavelength (CW) beams have been supplanted by ultra-short pulse deposition, which uses pulsed laser light to improve the surgical precision of the cut and limit the generation of thermal deformation at the periphery; also known as the heat-affected zone (HAZ). The efficacy of these ultra-short pulses makes them useful in delicate applications such as eye surgery and machining of medical devices such as stents.
Theoretically, this technology unlocks nanoscale levels of precision for cutting a wide range of materials (metals, polymers, etc.). However, its accuracy is dependent upon the instrumentation used to ensure precision motion control according to proprietary CAD files.
When it comes to cutting thick metal, recent advances in controlling the focus of the laser beam creating a “sawing” effect have shown encouraging results.
Precision Motion Control of Laser Cutters: Gantry Designs
A typical laser cutting array incorporates a high peak power solid-state laser head on the cross axis of the gantry. Linear motors drive the gantry in the XY axes while risers or an additional motorized linear stage allow vertical adjustment to the desired processing height. The challenge therein is providing both high speed and micrometer precision with long travel ranges to achieve high feature density on large-scale workpieces. High precision and high dynamic gantry systems with long travel ranges are routinely used to machine intricate stencils and printed circuit boards (PCBs).
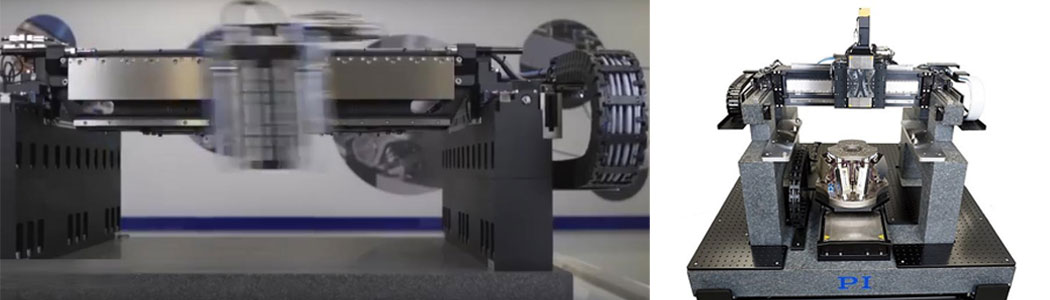
Precision Motion Control Systems from PI Physik Instrumente
PI offers high-performance gantry systems based on air-bearings, mechanical bearings or hybrid designs and controls for advanced laser machining in the photonics, electronics and medical industry. They boast extreme mechanical stability and a lightweight motion gantry with individual motors enabling long travel ranges of up to 2m in the longitudinal axis. Absolute linear encoders with 1nm resolution are integrated alongside all linear motors. The gantry system is controlled by an ACS-based precision motion controller that offers optimization for yaw control. This incorporates automated cross-axial tuning for consistent performance across all accessible areas of the gantry.
For precise vertical motion, PIMag linear motor stages with a pneumatic counterbalance are available. Especially in the case of air bearings, the service life of these gantries is outstanding, because there are no wearing components. In addition to the high precision and high operating throughput, the PI gantry system also eliminates time-consuming reference processes during start-up.
If you would like to learn more about our precision motion control systems for other laser processing applications, simply contact a member of the PI team today.
Lets join forces!
Talk to our Sales engineers about how we can support your solutions.