When it comes to high precision, granite-based, multi-axis motion systems, manufacturers have two fundamental options: Design a motion system where the granite base becomes an integral part, with bearings mounted directly on the granite slab and no need for a base plate – or, use off-the-shelf, discrete motion / positioning stages and mount them on a granite base or split-bridge granite structure.
The decision for each individual case depends on a number of factors which will be discussed below, as both of these multi-axis motion platform designs have specific advantages and limitations.
Each of these precision motion systems shown above consists of several stages, providing multi-axis motion. The 4-axis system on the left is designed for substrate and wafer inspection and has mechanical rails integrated on the granite base. By integrating rails on the granite base, a more compact and thermally stable system can be designed. In applications where the bearings / motors / encoders need to be protected from debris, integrated bellows with internally isolated double-walled structure with positive pressure air purge can be used on the lower axis while linear stages with sealed construction using hard covers, sealed sidebands, and positive pressure air purge can be used on the upper axes, as shown in the images on the center and right.
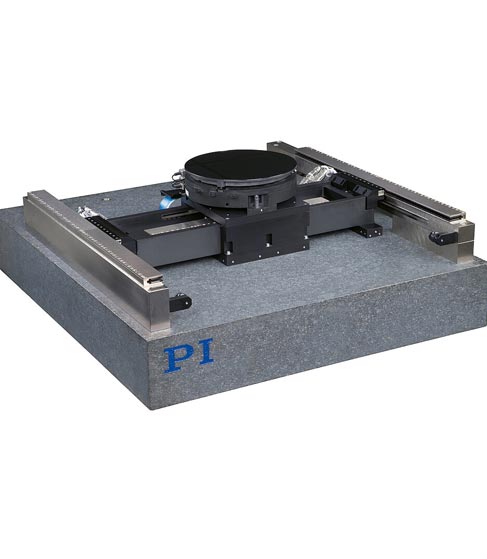
Z-axis Options: When the Z-axis is mounted on the XY-table, and relatively short travel is required, a wedge-type vertical translation stage is a great option, because it allows for 360-degree access and eliminates momentum loads on the horizontal axes, as is the case with a linear axis mounted vertically on a bracket. With split-bridge or gantry multi-axis positioning systems, the Z-axis is often mounted either directly on the bridge, on the bridge-mounted X-axis or on the gantry cross axis. Here, the ball-screw driven L-511 linear stage is often used in a vertical orientation, enhanced with a brake and an absolute encoder, because of its high resolution and payload. If higher speed vertical motion is required, linear motor stages can be used with mechanical counterbalance, air springs or magnetic weight force compensation to keep the current to the linear motors at close to zero unless acceleration or reaction to external forces is required.
Size and Form Factor: Rails-on-Granite vs Stage-on-Granite Multi-Axis Positioning Systems
This is where only small gains can be achieved with the integrated granite motion system design. Here, the base plate of the bottom stage is eliminated, dropping the height and center of gravity by a small amount. However, most of the other components from motors to sensors and cable tracks are identical.
The Effect of Reduced Center of Gravity on Abbe Errors, Stiffness, and Lifetime
By eliminating the base plate of the individual stages, working height can be reduced, along with a reduction in Abbe errors which has a positive effect on the work point positioning performance in more than one degree of freedom. At the same time, stiffness can be increased by eliminating one element between the granite base and the moving platform. This also results in a higher resonant frequency which will lead to better motion performance with reduced noise, at least when it comes to motion in the nanometer range. By mounting rails on granite, it is also easy to significantly increase the stage base width which has a big effect on XY flatness and straightness accuracy, load, and lifetime by reducing the bearing loads on the lower axis.
The Effect of Bearing Size / Spacing on Dynamics and Throughput, and Load Capacity
The type of mechanical bearings and air bearings that can be used in both designs, are similar, however when true planar XY motion is required: Air bearings are the only feasible solution, outside of flexure guides or magnetic levitation. If mechanical bearings are used, the rail on granite design allows for larger bearings without increasing the center of gravity and vertical height of the moving platform, compared to the stage on granite design, due to the elimination of the machined metal base. Using larger bearings at a wider spacing in the lower axis has multiple benefits in terms of roll stiffness, pitch stiffness, and yaw stiffness than an equivalent stage-on-granite multi-axis design. Increasing the angular stiffness of a multi-axis motion precision automation system allows for higher dynamics and increased overall throughput. Using larger bearings also allows for an increased load capacity, or longer service life, at identical load capacity.
Linear Motors, Screw Drives, Linear Encoders, Cable Management
No significant difference can be found between a stage-on-granite multi-axis positioning system compared to an integrated granite motion system. Motor output, acceleration, and position resolution are not affected by the different designs. The same is true for cable management, limit switches or mechanical hard stops.
Environmental Considerations, Protection from Debris – Laser Processing
Many discrete high performance linear stages, such as the V-417 linear motor stage, already come with hard covers, side seals, and air purge to protect (IP 50) against ingress of debris – important, for example, to protect bearings and encoders in laser processing applications or in general industrial environments with debris generating processes. This is where typically a standard linear stage might have an advantage relative to a rails-on-granite solution. However, it is possible to apply ingress protection features, such as wrapped bellows, double-walled construction, and air purges, to the rails-on-granite motion platform to protect the otherwise exposed bearings and encoders as shown in the concept below. While not an issue in cleaner environments, exposed bearings and encoders can be problematic when contamination is present.
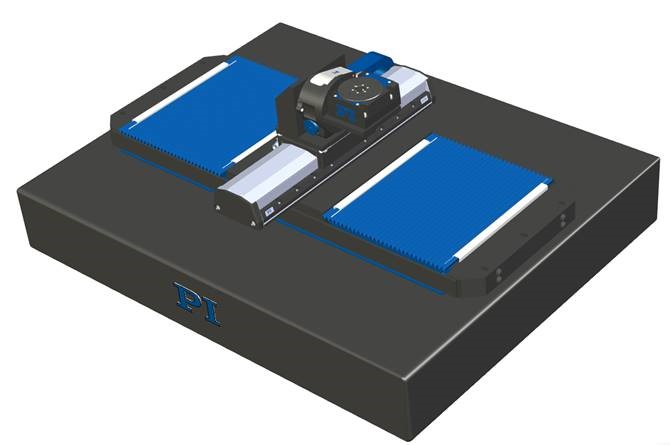
Serviceability / Maintenance
For multi-axis motion systems based on discrete stages, it is fairly easy to exchange individual axes, in case of maintenance. Direct drive, linear-motor stages usually have an extremely long service life, if bearings and motor are dimensioned according to the application requirements. Nevertheless, external events, e.g. a hard crash of other application related parts (robots, inadequate mounting of workpieces by the operator, etc.) with the motion system can make it necessary to service or replace a stage. Having a spare on hand, at the customer or at the manufacturer through a service contract reduces downtime and brings the machine back online in less time than it would take to replace and align individual components in a rails-on-granite motion system.
Cost Comparison of Integrated Granite Motion Systems vs Stage-on-Granite Motion Systems
Here, differences depend more in the type of customization and number of identical systems required by a customer. While some time and cost savings are to be expected when designing and building one single granite motion system using existing off-the-shelf discrete stages compared to a rail-on-granite motion system – when it comes to an order of multiple systems, the situation can easily change. Of course, we are talking about an apples-to-apples comparison, with identical performance specifications, load capacity, accuracy, speed, and dynamics ratings.
Integrated Granite Motion Systems and Multi-Axis Positioning Systems from PI
Talk to a PI engineer about your motion system requirements. PI is a leading global company with design and in-house manufacturing capabilities of a large number of critical technologies, components and mechatronics systems required to meet the complex nano-precision motion demands in industries such as semiconductors, electronics, optics, photonics, and aerospace.
- Air Bearings: PI makes its own air bearings and our teams have decades of experience in the design and assembly of high-end air bearing motion systems.
- Piezo Ceramics: We have a division specializing on piezo ceramics optimized for high reliability motion, vibration cancellation and nanopositioning applications
- Direct Drive Motors: We design custom electromagnetic and non-magnetic ceramic motors for our motion systems.
- High-end Motion Controllers: Our ACS advanced industrial motion controllers are world famous for their performance and flexibility.
- Parallel-kinematic Hexapod Motion Systems: PI started designing and manufacturing hexapods for precision optical information in the early 1990s.
- Positioning Sensors with Sub-Nanometer Resolution: PI designs several digital and analog nanopositioning sensors for our standard and custom motion systems.
Thanks to our experience and continuous innovation (more than 500 patents / patent applications), PI can provide the most advanced precision motion control solution for automation from actuators with force and position control to multi-degree-of freedom custom motion platforms with mixed technologies. In addition to the motion hardware and motion control electronics, we also offer software, for example to control lasers and galvo scanners or dispensers for additive manufacturing. For more than 50 years, PI has been a reliable partner for the most innovative companies in the world, enabling them to push boundaries beyond the state-of-the-art.